La realidad es que ninguna operación de soldadura produce ensamblajes perfectos todo el tiempo. Incluso los componentes de mayor calidad fallan de vez en cuando. Por eso es tan importante entender los mejores métodos y materiales de reparación y repaso para quienes fabrican, mantienen o reparan placas de circuitos impresos (PCB).
¿Cuál es la forma más segura de manipular las PCB cuando se reparan?
Hay que tener cuidado al manipular las placas de circuito impreso (PCB) para evitar causar más daño del que se está reparando. Estas son algunas de las cuestiones de las que hay que preocuparse:
- Use anteojos de seguridad: la soldadura puede salpicar o los cables pueden volar cuando se recortan, así que utilice anteojos de seguridad para protegerse los ojos en cualquier momento en que esté reparando una PCB.
- Desenchufe y descargue sus aparatos electrónicos: para evitar un cortocircuito en los aparatos electrónicos y la posibilidad de que usted mismo se electrocute, asegúrese de que el dispositivo que está reparando esté desenchufado y totalmente descargado. Los condensadores y las fuentes de alimentación pueden contener carga, por lo que debe prestar especial atención para asegurarse de que estén completamente descargados. Si hay alguna batería adicional, desconéctela también.
- Prevenga las descargas electrostáticas: una descarga electrostática es el flujo repentino de electrones, o una chispa, de una superficie a otra. Se produce por un diferencial entre las dos superficies, de modo que una tiene más electrones que la otra. A la naturaleza le encanta el equilibrio, así que los electrones se intercambian para igualar su distribución. Llevar una pulsera con conexión a tierra y trabajar sobre un tapete con conexión a tierra es la mejor manera de prevenir las descargas electrostáticas. Una pulsera tiene una superficie conductora que toca la piel, por lo que puede desangrar el exceso de electrones. Un tapete seguro frente a las descargas electrostáticas funciona con un principio similar, por lo que expulsa una carga de cualquier cosa en su superficie. Si trabaja en una computadora, puede sujetar la correa directamente a una zona sin pintar de la caja.
- Reduzca la contaminación lavándose las manos y manipulando solo los bordes de la PCB: contaminarse con las manos puede causar problemas de soldabilidad y posiblemente provocar fallos en la placa por corrosión o crecimiento dendrítico. La silicona en la loción para manos o recogida de algún lugar puede crear una barrera en las zonas de contacto, que en un proceso de soldadura, podría impedir que la soldadura creara una buena unión metalúrgica. La soldadura puede pegarse temporalmente, pero se desprende cuando se expone a cualquier tipo de estrés térmico o físico. La contaminación, como la sal en las papas fritas que se comió con el almuerzo, es otra causa principal de los problemas introducidos en el proceso de reparación. La sal es un sustrato iónico, que cuando se combina con la humedad del aire, puede causar corrosión. Las partículas iónicas también pueden unirse para formar dendritas, lo que puede provocar fugas de corriente e incluso cortocircuitos. Lavarse las manos y usar solo loción para manos con seguridad electrónica es una buena manera de prevenir este tipo de fallo de la placa. Además, sujetar la placa solo por los bordes sin contactos (por ejemplo, los dedos de oro) puede ayudar a evitar que se deposite la contaminación en cualquier zona crítica.
¿Debería preocuparme por la electricidad estática al manipular las PCB?
Sí. Un técnico típico que trabaja en una PCB puede generar miles de voltios. Los dispositivos lógicos SMOS pueden dañarse con tensiones de entre 250 y 3000 voltios, los dispositivos EPROM con tensiones de hasta 100 voltios y los chips microprocesadores con tensiones de hasta 10 voltios. El daño puede interrumpir las funciones o crear problemas intermitentes, y puede ser catastrófico (inmediato) o latente (más tarde, como en los "fallos de campo"). (fuente: libro de hardware informático de Phil Storrs)
Los electrones se intercambian constantemente a medida que los objetos interactúan entre sí. Los problemas surgen cuando los materiales en cuestión no permiten que los electrones fluyan fácilmente y alcancen el equilibrio. Llamados aislantes, tienden a recoger electrones, que crean puntos calientes cargados negativamente en su superficie.
Cuando estos puntos calientes cargados se acercan (pero ni siquiera están en contacto directo) a otro objeto, puede producirse un intercambio o "descarga" repentina, en la que los electrones se intercambian repentinamente para crear un equilibrio. Ese fenómeno se denomina "descarga electrostática" o "ESD".
Las descargas electrostáticas se producen todo el tiempo, especialmente en climas secos y en la temporada de invierno, cuando no hay humedad en el aire que ayude a expulsar el exceso de electrones (el agua es conductora, por lo que permite que los electrones fluyan más fácilmente). Normalmente no es más que una irritación, pero con los aparatos electrónicos sensibles, se pueden producir fallos en las PCB.
Llevar una pulsera con conexión a tierra y trabajar en un tapete con conexión a tierra es la mejor manera de prevenir las descargas electrostáticas. Una pulsera tiene una superficie conductora que toca la piel, por lo que puede expulsar el exceso de electrones. Un tapete seguro para las descargas electrostáticas funciona según un principio similar, por lo que expulsa una carga de cualquier cosa en su superficie. Si trabaja en una computadora, puede sujetar la correa de la muñeca directamente a una zona sin pintar de la caja.
La pulsera con conexión a tierra expulsa el exceso de electrones para prevenir descargas estáticas dañinas.
¿Cómo reduzco el estrés térmico en los componentes con la reparación o repaso de una PCB?
El objetivo es calentar y eliminar la unión soldada y retirar el componente lo más rápido posible, y evitar calentar las áreas circundantes lo máximo posible. Calentar solo las uniones soldadas necesarias para eliminar los componentes defectuosos y realizar la tarea rápidamente y con un solo intento reduce el estrés térmico en otras zonas. La mecha de soldadura o las unidades de desoldadura son buenos métodos para eliminar la soldadura de zonas aisladas. Los métodos que utilizan placas calientes o aire caliente presentan una mayor probabilidad de provocar un fallo de la PCB más adelante.
¿Cómo se puede eliminar la soldadura o los componentes de una PCB?
¿Se puede eliminar la soldadura?
¿Cómo se arreglan los errores de soldadura?
La soldadura es un concepto bastante simple de combinar dos superficies metálicas mediante un soldador caliente, un fundente y una soldadura. Quitar la misma soldadura si algo no funciona es más complicado. Puede que haya que quitar y reemplazar los componentes defectuosos, o que haya que eliminar el exceso de soldadura, como en el caso de los puentes entre dos contactos.
Los siguientes son métodos comunes de remoción de soldadura, también llamados "desoldadura":
- Mecha de soldadura: mecha de soldadura, trenza de desoldadura o simplemente "mecha" son términos que se utilizan para designar una trenza de cobre que se utiliza para absorber la soldadura. Generalmente está recubierta de fundente, por lo que cuando se calienta, la soldadura se funde, se estira y se retiene mediante una combinación de acción humectante y capilar. La mecha de soldadura le permite eliminar la soldadura en zonas aisladas sin someter a estrés térmico a la placa en general o a los componentes cercanos. La mecha de soldadura solo puede eliminar la soldadura expuesta, por lo que los componentes que cubren las zonas de contacto, como los conjuntos de rejillas de bolas (BGA), se tienen que eliminar antes de que se pueda eliminar la soldadura residual.
- Aspiradores de soldadura: los aspiradores de soldadura utilizan un vacío con resorte para extraer la soldadura fundida. La soldadura debe fundirse con un soldador o con aire caliente, como en una pistola de calor o un puesto de repaso. Solo se extraen pequeñas cantidades de soldadura a la vez, o a menudo se necesitan múltiples intentos para eliminar un componente. Mantener la temperatura de la soldadura o volver a fundir una unión de soldadura aumenta la tensión térmica de los componentes, de otras uniones de soldadura y de la placa de circuitos en general. Los aspiradores de soldadura solo pueden eliminar la soldadura expuesta, por lo que los componentes que cubren las zonas de contacto, como los conjuntos de rejilla de bolas (BGA), se tienen que eliminar antes de que se pueda retirar la soldadura residual.
- Puestos de desoldadura: los puestos de desoldadura tienen una punta de soldadura con un agujero en el medio que atrae la soldadura una vez que se derrite. Aunque es un método muy eficaz para desoldar, los puestos de repaso solo pueden eliminar la soldadura expuesta, por lo que los componentes que cubren las zonas de contacto, como los conjuntos de rejillas de bolas (BGA), se tienen que eliminar antes de que se pueda retirar la soldadura residual.
- Puestos de soldadura de aire caliente: estos puestos soplan aire caliente sobre la zona de reparación para fundir la soldadura, y el componente se retira con pinzas o con un elevador de vacío. Una vez que se quita el componente, la soldadura tendrá que eliminarse de otra manera.
- Pinzas calientes: si se imagina agarrando las zonas de cable con una pinza hecha de dos soldadores, podrá tener una idea general. La cuestión es sujetar los cables de ambos lados del componente para derretir toda la soldadura a la vez. Esto limita el estrés térmico general en comparación con el aire caliente. Una vez que el componente se ha apartado, la soldadura tendrá que eliminarse de otra manera.
- Placa caliente: al colocar la PCB en una placa caliente se funden (o refluyen) todas las uniones de soldadura para permitir que se eliminen varios componentes al mismo tiempo. Este método puede someter innecesariamente a tensión a otros componentes y a la placa en su conjunto.
¿Qué es la mecha de soldadura?
Mecha de soldadura, trenza de desoldadura o simplemente "mecha" son términos que se utilizan para designar una trenza de cobre que se utiliza para absorber la soldadura. Generalmente está recubierta de fundente, por lo que cuando se calienta, la soldadura se funde, se estira y se retiene mediante una combinación de acción humectante y capilar. La mecha de soldadura le permite eliminar la soldadura en zonas aisladas sin someter a estrés térmico a la placa en general o a los componentes cercanos. La mecha de soldadura solo puede eliminar la soldadura expuesta, por lo que los componentes que cubren las zonas de contacto, como los conjuntos de rejillas de bolas (BGA), se tienen que eliminar antes de que se pueda eliminar la soldadura residual.
La mecha de soldadura se presenta en una amplia variedad de grosores para eliminar de manera eficaz la soldadura de diferentes tipos de zonas de contacto. La mecha de soldadura generalmente viene recubierta con un fundente que se puede ajustar a su proceso de soldadura original: resina, sin limpiar o sin fundente para añadir su propio fundente a medida que lo usa.
Cerca de mecha de soldadura de cobre
¿Cómo uso la mecha de soldadura?
- Coloque la trenza sobre la soldadura no deseada, preferiblemente sobre la mayor acumulación de soldadura, de manera que maximice el contacto de la trenza con la superficie de la soldadura.
- A continuación, coloque la punta del hierro sobre la mecha a 45 grados y permita que el calor se transfiera a la almohadilla. La soldadura fundida se absorberá en la trenza.
- Mueva la punta de la soldadura y la trenza según sea necesario para eliminar toda la soldadura a la vez. Tenga cuidado de no arrastrar la trenza sobre las almohadillas, que pueden rayarse.
- Una vez que la trenza esté completamente soldada, debe eliminar la parte sobrante y pasar a la trenza nueva para poder extraer más soldadura. Retire la placa y la trenza simultáneamente para evitar soldar el cable a la placa.
¿Por qué hay tantos tipos diferentes de mecha de soldadura?
La mecha de soldadura se presenta en una amplia variedad de grosores para eliminar de manera eficiente la soldadura de diferentes tipos de zonas de contacto y está recubierta con una variedad de fundente que se puede adaptar a su proceso de soldadura original.
Tamaños habituales de la mecha de soldadura:
Una mecha demasiado fina no eliminará suficiente soldadura y lo obligará a recortar y volver a fundir la soldadura una y otra vez. Una mecha demasiado ancha tarda más en calentarse y puede interferir con otros componentes de la placa de circuito.
Elija un ancho de trenza de desoldadura que se ajuste al tamaño de la zona de contacto. Esto asegurará que consiga una conducción de calor adecuada y que no desolde zonas no deseadas. El ancho del alambre desoldado se designa con los números del 1 al 6 o códigos de color, que son la norma del sector.
- #1/La trenza blanca es la más pequeña (menos de 1 mm de ancho) y es principalmente para dispositivos de montaje superficial y microcircuitos.
- A la mayor parte de la gente le parece que el #2/amarillo, #3/verde y #4/azul es el cable desoldador más común.
- El #5/marrón es ideal para eliminar grandes bloques de soldadura y el #6/rojo es mejor para desoldar almohadillas o terminales BGA.
- Mantenga tres o cuatro anchos diferentes en su zona de trabajo para abarcar todos los casos.
- La mecha se puede doblar o recortar en un ángulo para que se ajuste mejor a la zona de contacto.
Bobina resistente a las descargas electrostáticas para mecha de soldadura de 5 y 10 pies.
La bobina común para las longitudes de mecha de soldadura a granel
Tipos comunes de revestimiento de fundente en la mecha de soldadura:
- Colofonia: la trenza de colofonia tiene la acción de mecha más rápida pero deja residuos que hay que limpiar a fondo.
- Sin limpieza: la trenza fundida sin limpieza es ideal cuando la limpieza no es practicable o no resulta posible. Después de desoldar, lo único que queda es un residuo claro y no iónico. Para el trabajo de campo, cuando una limpieza a fondo es más exigente, este es el tipo de trenza que se debe usar.
- Sin fundente: en un entorno de producción o reparación donde el fundente está especificado y no se puede cambiar, o cuando se necesita un fundente acuoso, puede añadir su propio fundente a este tipo de trenza. La mecha sin fundente no quitará la soldadura a menos que se añada el fundente. Diferentes tipos de fundentes están disponibles en embalajes de rotuladores, lo cual es ideal para fundir una trenza.
- La mecha de soldadura también se puede empacar en varias longitudes. Las longitudes de 5 pies y 10 pies son útiles para su uso en una mesa de trabajo. Los carretes disipadores de estática, también llamados "bobinas", existen para evitar dañar los componentes sensibles a las descargas electrostáticas. Los carretes más largos, como los de 25 pies (7,6 m), 50 pies (15,2 m), 100 pies (30,5 m) y 500 pies (152,4 m), suelen almacenarse en un lugar más centrado y se suministran a los técnicos cuando es necesario.
- También se dispone de otros diseños de trenzas especializadas. Por ejemplo, Chemtronics ofrece Soder-Wick sin plomo, que está diseñado para calentarse más rápido, de modo que se minimiza el choque térmico para aplicaciones sin plomo de gran calor.
¿Puedo añadir mi propio fundente a la mecha de soldadura?
En un entorno de producción o reparación donde el fundente se especifica y no se puede cambiar, o cuando se necesita un fundente acuoso, se puede añadir su propio fundente a este tipo de trenza. La mecha sin fundente no quitará la soldadura a menos que se añada el fundente. Existen distintos tipos de fundentes disponibles en envases de rotulador, que son ideales para fundir una trenza.
Por ejemplo, Chemtronics ofrece los siguientes rotuladores de fundente:
- Rotuladores de fundente sin limpieza: este fundente sin limpieza está formulado para funcionar a las elevadas temperaturas de la soldadura sin plomo, pero también es efectivo para la soldadura de estaño-plomo. Está diseñado con una baja tensión superficial para evitar la formación de puentes. La limpieza posterior a la soldadura es opcional, ya que el ligero residuo que queda después de la soldadura es apenas perceptible, no es corrosivo y no contiene haluros. Esta es una buena opción para la soldadura de estaño-plomo, donde se debe evitar la limpieza.
- Rotulador de fundente de colofonia: se trata de un fundente de colofonia de alto contenido en sólidos tipo R que proporciona una excelente capacidad de soldadura en una amplia variedad de aplicaciones. El residuo que queda no es corrosivo y no contiene haluros, pero es mejor eliminar el residuo después de la soldadura por razones estéticas.
- Rotulador de fundente soluble en agua: es un fundente ORH1 de pH neutro muy activo. Permite soldar fácilmente tanto las soldaduras sin plomo como las que lo contienen. Este fundente se debe limpiar y se puede quitar fácilmente con agua desionizada, como en un sistema por lotes o en línea, o la limpieza de la mesa de trabajo con el extractor de fundente soluble en agua Flux-Off®.
Seis consejos para una desoldadura eficiente y de alta calidad.
- Mantenga la punta de su soldador limpia y estañada para una conducción efectiva del calor.
Esto puede parecer obvio, pero a menudo se pasa por alto y es fundamental para una desolación eficaz. Las puntas del soldador cubiertas con fundente quemado y oxidación no se mojarán (aceptarán la soldadura) y conducirán el calor de forma deficiente. Una punta de soldadura limpia y estañada conduce mejor el calor a través de la trenza de desoldadura e inicia la acción de desoldadura más rápidamente.
- Minimice el tiempo que la placa y los componentes permanecen a alta temperatura.
La aplicación de altos niveles de calor a la placa o sus componentes durante un periodo de tiempo prolongado puede dañar la placa, los componentes, crear uniones de soldadura quebradizas y provocar problemas de mantenimiento a lo largo del ciclo.
- Adapte el ancho de la trenza a la junta de soldadura o a la almohadilla de contacto.
La trenza desoldadora por lo general se presenta en diferentes anchos para que pueda hacer coincidir la trenza con lo que se está desoldadando. Una mecha que sea demasiado delgada no eliminará suficiente soldadura y le obligará a recortar y volver a fundir la soldadura una y otra vez. Una mecha demasiado ancha tarda más en calentarse y puede interferir con otros componentes de la placa de circuito.
- Combine la punta del soldador con el ancho de la trenza para mayor precisión.
Utilice una punta de soldadura que sea aproximadamente del ancho de la trenza y de la zona de contacto. Una punta que es demasiado pequeña exigirá un mayor tiempo de permanencia. Una punta demasiado grande corre el riesgo de exponer otros componentes en un conjunto denso. Hacer coincidir la punta le permite fundir la soldadura no deseada más rápido y minimiza el tiempo en que se aplica el calor. Use una cuchilla o punta de cuchillo cuando desolde grandes zonas, como una almohadilla BGA.
- Compare el tipo de fundente con su proceso de limpieza
La trenza desoldadora está disponible en varios tipos de fundente según su proceso de limpieza y otros requisitos. La trenza con fundente de colofonia tiene la acción de mecha más rápida, pero deja residuos que hay que limpiar a fondo. La trenza fundida sin limpieza es ideal cuando esta no es practicable o no resulta posible. Después de desoldar, lo único que queda es un residuo claro y no iónico. Para el trabajo de campo, cuando la limpieza a fondo es más exigente, este es el tipo de trenza a utilizar.
- Proteja su placa contra la corrosión mediante un extractor de fundente de calidad
Los residuos de fundente pueden causar crecimiento dendrítico y corrosión en los ensamblajes de PCB, así que asegúrese de emplear las mejores prácticas y limpiar la placa. Después de que todos los componentes se hayan reemplazado y se haya eliminado el exceso de soldadura, limpie completamente la zona con un extractor de fundente de calidad.
¿Cómo elimino el exceso de soldadura de las almohadillas BGA después de quitar el componente de la PCB?
Las grandes cantidades de soldadura en las grandes almohadillas o conjuntos de rejilla de bolas (BGA) pueden eliminarse utilizando un aspirador de soldadura y aire caliente, pero para ello es necesario exponer la PCB a altas temperaturas durante un periodo de tiempo prolongado, lo que puede someter a estrés térmico a otros componentes y a la placa en su conjunto.
La mecha de soldadura es un método más rápido y menos estresante desde el punto de vista térmico para eliminar la soldadura de una gran superficie. La mecha de soldadura está disponible en configuraciones más amplias, de 3 a más de 5 mm. De 3,5 a 4 mm de ancho se identifica como #5 o mecha marrón, y de 5 a 5,5 mm como #6 o mecha roja. La geometría de la punta de la soldadura debe ajustarse lo más posible al ancho de la mecha. Las puntas con una gran superficie plana, como un destornillador, un cincel, un bisel o una cuchilla, suelen funcionar mejor. Muchos técnicos cometen el error de sostener la punta de la soldadura en la superficie de la trenza y luego arrastrar la trenza a través de las almohadillas para eliminar la soldadura fundida. El movimiento de arrastre puede rayar la superficie de las almohadillas o el revestimiento de la OSP. La siguiente técnica es la mejor práctica que recomendamos:
- Aplique la trenza sobre las almohadillas para desoldar.
- Aplique la punta de soldadura caliente en un extremo de la trenza (paso 2).
- Manteniendo la trenza quieta, arrastre la punta de soldadura hacia arriba de la trenza (pasos 3 y 4). No es necesario aplicar presión sobre el hierro. Solo se corre el riesgo de jalar la trenza y de rayar las almohadillas. El peso del soldador debería ser suficiente para hacer el trabajo.
- Levante la trenza mientras aún está caliente y repita los pasos anteriores en la siguiente fila de almohadillas (paso 5). Asegúrese de recortar la trenza gastada antes de seguir con este paso. El exceso de trenza actúa como disipador de calor, por lo que tardará más tiempo en calentarse.
¿Cómo se limpia la PCB después de la soldadura?
¿Cómo se elimina el fundente de soldadura?
La forma más frecuente de limpiar los residuos de fundente de una zona de reparación es saturar un hisopo de algodón o de espuma con alcohol isopropílico u otro disolvente de limpieza y frotarlo alrededor de la zona de reparación. Aunque esto puede ser adecuado para el fundente sin limpieza, donde el objetivo es una PCB visualmente limpio, puede no ser lo suficientemente limpio cuando se trata de fundentes de mayor activación, como RA o acuosos. El secreto es que los residuos de fundente no se evaporarán junto con el disolvente. Puede disolver el fundente, y algunos de los residuos se empaparán en el hisopo, pero la mayoría de los residuos se asentarán de nuevo en la superficie de la placa. Muchas veces estos residuos blancos son más difíciles de eliminar que el fundente original.
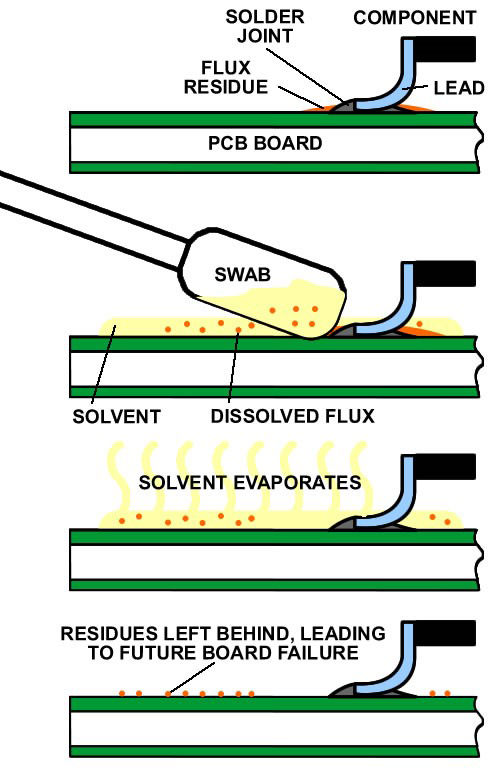
Una mejora rápida y fácil de este proceso es enjuagar la placa después de limpiar la zona de reparación. Mientras el disolvente está todavía húmedo, rocíe toda la placa con un limpiador de fundente en aerosol. Sostenga la PCB en un ángulo para permitir que el disolvente fluya sobre la placa y se escurra, junto con cualquier residuo que se recoja.
El accesorio de paja que se suministra con los extractores de fundente en aerosol es una excelente manera de incrementar la fuerza de pulverización y de penetrar bajo los componentes.
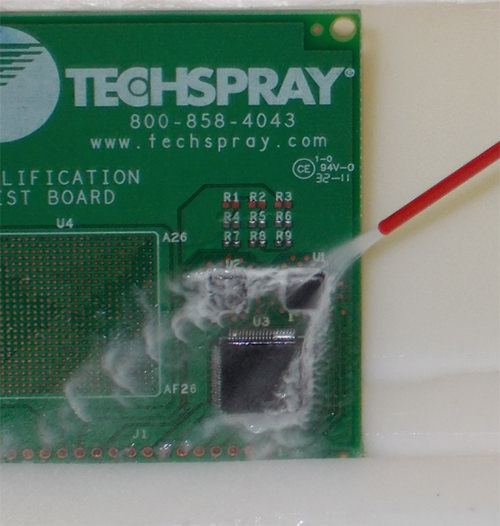
El aerosol con paja sirve para limpiar los componentes inferiores
Chemtronics ofrece el sistema BrushClean con muchos de sus extractores de fundente. El disolvente limpiador se rocía a través del cepillo, por lo que la agitación se puede aumentar restregando mientras se rocía. Para absorber los residuos de fundente, se puede colocar un limpiador de policelulosa sin pelusa sobre la zona de reparación y se puede pulverizar y frotar el material. Luego se retira el accesorio de limpieza y cepillado y se rocía sobre la placa para realizar el enjuague final.
La fijación del cepillo de aerosol sobre un limpiador disuelve y absorbe los residuos de fundente al mismo tiempo.
¿Cómo se conecta un componente sensible a la temperatura sin soldadura de alta temperatura?
El epoxi conductor de dos partes es una gran solución para establecer conexiones electrónicas sin soldadura. Este tipo de epoxi contiene material conductor, por lo que cuando se cura, forma una unión muy fuerte y altamente conductora, similar a una unión soldada. Chemtronics ofrece dos opciones: CircuitWorks® Epoxi conductor, que se cura en 10 minutos, y CircuitWorks® Epoxi conductor de 60 minutos, que proporciona más tiempo de trabajo. Ambos epoxis tienen componentes A y B que se deben mezclar bien antes de que comience el proceso de curado. Una vez mezclados, se utiliza la púa de plástico incluida para aplicar el epoxi a la conexión. Si es posible el movimiento durante el proceso de curado, tendrá que pegar con cinta adhesiva o asegurar de otra manera los cables o componentes.
¿Cómo se quita el revestimiento de conformación cuando se repara o se repasa una PCB?
El mejor método para eliminar un revestimiento depende del tipo de revestimiento y de la sensibilidad de los componentes:
- Acrílico (AR) / Silicona (SR) / Revestimientos de uretano (UR):
Al desoldar, es frecuente que simplemente se quemen estos revestimientos. Esto podría dejar los bordes quemados o ásperos que será necesario limpiar antes de volver a revestir. Estos revestimientos se pueden eliminar químicamente, usando disolventes especializados o disolventes comunes como la acetona, el tolueno y el xileno. Todos ellos son muy duros (por lo que disuelven muy bien los revestimientos) y el tolueno y el xileno tienen problemas de toxicidad, por lo que hay que asegurarse de llevar el equipo de protección personal (EPP) apropiado y tener una ventilación adecuada.
Chemtronics ofrece el rotulador extractor de revestimientos de conformación CircuitWorks®, que permite eliminar una zona de revestimiento apretada alrededor de una zona de reparación sin perjudicar el resto de la PCB. Primero se satura la punta golpeándola ligeramente sobre una superficie, lo que abre la válvula y libera el disolvente. Si se mantiene la punta hacia abajo, se puede sobresaturar, lo que podría hacer que el disolvente fluyese hacia zonas no deseadas.
Luego se frota la punta del rotulador sobre el revestimiento que se quiere quitar. Es posible que tenga que limpiar periódicamente la punta del rotulador con un limpiador para eliminar la resina acumulada. La punta continuará resaturándose a medida que aplique presión mientras limpia. No es necesario presionar con fuerza la punta del rotulador, pues esto podría hacer que el disolvente fluyera en exceso sobre la placa. Deje que el disolvente haga el trabajo, y dele el tiempo necesario para descomponer la resina del revestimiento. El revestimiento acrílico se descompondrá rápidamente, pero la silicona y especialmente el uretano tardarán más tiempo.
- Resina epoxy (ER) / parileno (XY):
Los revestimientos de epoxi y parileno son revestimientos increíblemente firmes, y resistentes a las tensiones físicas y químicas. Por supuesto, las propiedades que hacen que sean tan eficaces también los hacen difíciles de eliminar. No se pueden quitar estas resinas con un producto químico. Es posible quemarlas o derretirlas, pero también se corre el riesgo de dañar la PCB. El método de chorreado microabrasivo suele ser la forma aceptada de eliminar los revestimientos de epoxi y parileno.
El chorro microabrasivo utiliza un dispositivo especializado para soplar las partículas abrasivas sobre la superficie revestida. El medio abrasivo debe elegirse con mucho cuidado para que el proceso no dañe la superficie o los componentes y elimine las marcas. La zona alrededor de la reparación se debe enmascarar para aislar el efecto de la voladura.
- Revestimiento ultrafino (UT):
La capa ultradelgada, que es cada vez más frecuente en los aparatos electrónicos de consumo, como los celulares, no tendría que ser eliminada. Es invisible a simple vista, y se quema y raspa fácilmente.
¿Cómo parcheo el revestimiento de conformación después de la reparación de una PCB?
Lo ideal sería utilizar el mismo material de revestimiento que el montaje original de la placa de circuito impreso, que debería especificarse en el manual de mantenimiento del dispositivo. En la práctica de la reparación de aparatos electrónicos, puede que no tenga ni idea de lo que se aplicó originalmente. En ese caso, la solución más fácil es revestirla con una capa de acrílico.
Chemtronics ofrece rotuladores de revestimiento CircuitWorks® en diversos colores para que coincidan con la resistencia de la PCB. Los rotuladores de revestimiento son básicamente un revestimiento acrílico conformado en un cómodo embalaje, y la versión transparente se puede utilizar para revestir zonas pequeñas. Simplemente presione la punta del rotulador y apriete el tubo para dispensar el material de revestimiento. Para zonas más grandes, el revestimiento de conformación se puede aplicar con un pequeño pincel de ácido.
Independientemente de la forma en que se aplique el revestimiento, asegúrese de evitar revestir los conectores, ya sea aplicando un revestimiento a su alrededor o enmascarándolos con cinta Kapton o una máscara de soldadura temporal.
¿Cómo se repara un rastro roto en una PCB?
Un método habitual para reparar un rastro roto es soldar un puente, que es básicamente un cable de derivación alrededor del rastro roto. Esto puede ser demasiado lento y visualmente poco atractivo. Chemtronics ofrece los rotuladores conductores CircuitWorks®, que contienen un material altamente conductor como la plata o el níquel suspendido en un polímero líquido. Estos rotuladores permiten volver a trazar el rastro, básicamente.
Estos son los pasos para reparar de forma rápida y efectiva un rastro con un rotulador conductor:
- Para una buena continuidad eléctrica, es necesario que exponga alguna superficie del rastro original. Si hay resistencia de soldadura hasta la rotura, use una cuchilla afilada para raspar una porción de 1/16 de pulgada de la resistencia.
- Limpie la zona con un hisopo saturado con un limpiador solvente como el alcohol isopropílico (IPA) o con un rotulador extractor de fundente CircuitWorks®.
- Sacuda vigorosamente el rotulador conductor hasta que oiga la vibración de la bola interna.
- Presione la punta del rotulador en la zona de rotura y apriete el tubo del rotulador para dispensar la tinta conductora.
- Deje que la tinta conductora se cure al menos una hora antes de reparar el revestimiento.
- Utilice un lápiz de revestimiento de CircuitWorks para reparar la zona de la resistencia en la superficie de rotura. Los rotuladores de revestimiento se presentan en diversos colores para que coincidan con el color de la PCB. Presione la punta del rotulador y apriete el tubo para dispensar el material de revestimiento.
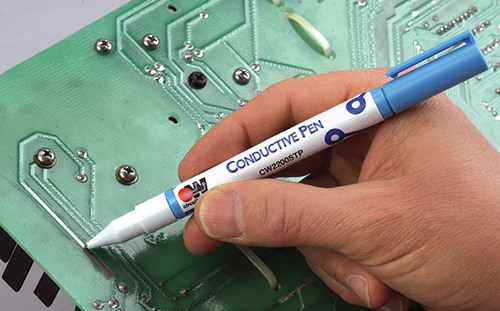
¿Cómo se reparan las roturas en el blindaje de EMI o RF?
La pintura conductora CircuitWorks es un polímero de un solo componente, relleno de plata, que se seca en cuestión de minutos a temperatura ambiente, lo que la convierte en una solución ideal para el parcheo del blindaje EMI/RFI. El kit incluye pinceles, hisopos y una púa de plástico para reparar zonas grandes y pequeñas.
En el caso de la pantalla metálica y la malla de alambre, es importante que los agujeros de la pantalla o la malla sean significativamente más pequeños que la longitud de onda de la radiación electromagnética que queda fuera. El objetivo de tales diseños de malla es mantener un patrón de agujeros coherente con un material conductor para asegurar la continuidad eléctrica. Dicha malla se puede reparar restaurando el patrón de agujeros con cinta de poliamida y pintura conductora CircuitWorks.
Simplemente aplique la cinta de poliamida al interior de la malla y restaure cuidadosamente el patrón de la malla con el CW2205. Es importante asegurarse de que se mantenga el contacto entre la malla y la pintura conductora. Se puede aplicar una segunda capa de cinta de poliamida en el lado opuesto para aumentar la durabilidad. Dado que la cinta de poliamida es invisible a los campos electromagnéticos en estas longitudes de onda, la cinta de poliamida puede permanecer y se restaura el escudo EMI.La malla de la pantalla dañada se puede reparar con cinta de poliamida y pintura conductora.
Otra situación habitual es que la lámina de aluminio del interior del cable blindado esté dañada. Como en el caso anterior, esto provocará una pérdida de continuidad y podría volver a permitir la interferencia electromagnética. En este caso, una reparación sencilla consiste en arreglar el agujero o el desgarro con cinta de poliamida y luego usar la pintura conductora CircuitWorks para pintar la cinta y restaurar la continuidad.
¿Cómo repara una almohadilla dañada en una PCB?
El epoxi estándar de dos partes puede contaminar la superficie del conector, lo que genera una barrera aislante. El epoxi conductor de dos partes es una gran solución para hacer la reparación de las almohadillas dañadas. Este tipo de epoxi contiene material conductor, por lo que cuando se cura, forma una unión muy fuerte y altamente conductora, similar a una unión de soldadura. Chemtronics ofrece dos opciones: el epoxi conductor CircuitWorks®, que se cura en 10 minutos, y el epoxi conductor CircuitWorks®, de 60 minutos, que proporciona un mayor tiempo de trabajo. Ambos epoxis tienen componentes A y B que se deben mezclar bien antes de que comience el proceso de curado. Una vez mezclados, deberá utilizar la púa de plástico incluida para aplicar el epoxi a la conexión.
Para reparar una almohadilla levantada:
- Limpie la zona con un hisopo saturado de un limpiador de disolventes como el alcohol isopropílico (IPA) o un rotulador extractor de fundente CircuitWorks.
- Aplique el epoxi conductor mezclado debajo de la almohadilla con la púa de plástico suministrada.
- Presione hacia abajo la almohadilla.
- Deje que el epoxi se cure completamente antes de soldarlo a la almohadilla.
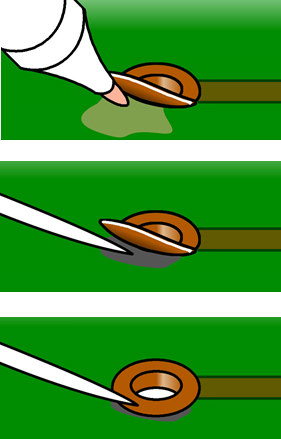
Para reemplazar una almohadilla dañada:
- Corte la almohadilla dañada.
- Para una buena continuidad eléctrica, necesita que quede expuesta alguna superficie del rastro original. Si hay resistencia de soldadura hasta la rotura, use una cuchilla afilada para raspar una porción de 1/16 de pulgada de la resistencia.
- Limpie la zona con un hisopo saturado con un limpiador de disolventes como el alcohol isopropílico (IPA) o con un rotulador extractor de fundente CircuitWorks.
- Aplique el epoxi conductor mezclado debajo de la almohadilla con la púa de plástico suministrada.
- Presione hacia abajo la almohadilla.
- Aplique más epoxi entre el reemplazo de la almohadilla y el rastro expuesto.
- Deje que el epoxi se cure completamente antes de soldar la almohadilla.
Para reparar sin un sustituto de la almohadilla:
- Corte la almohadilla dañada.
- Para una buena continuidad eléctrica, necesita que quede expuesta alguna superficie del rastro original. Si hay resistencia de soldadura hasta la rotura, use una cuchilla afilada para raspar una porción de 1/16 de pulgada de la resistencia.
- Limpie la zona con un hisopo saturado con un limpiador de disolventes como el alcohol isopropílico (IPA) o con un rotulador extractor de fundente CircuitWorks.
- Aplique el epoxi conductor mezclado debajo de la almohadilla con la púa de plástico suministrada.
- Coloque el componente de plomo en el epoxi. En el caso de un cable con agujero pasante, se puede formar un ala de gaviota improvisada o un cable en J para proporcionar más superficie de agarre al epoxi. Se puede aplicar más epoxi sobre el plomo para mayor seguridad.
- Deje que el epoxi se cure completamente antes de manipular la PCB.
¿Cómo se repara una grieta de la PCB o una zona abierta de la resistencia de la soldadura en una PCB?
Esta respuesta supone que la grieta no afecta a los rastros de la superficie o de la capa interna. El recubrimiento con epoxi proporciona una reparación resistente que puede reforzar las áreas de placas de circuitos impresos con más grietas estructurales. Usar:
- Limpie la zona con un hisopo saturado de un limpiador de disolventes como el alcohol isopropílico (IPA) o un rotulador extractor de fundente CircuitWorks.
- Mezcle cantidades iguales (1:1) por volumen de la Parte A y la Parte B. Mezcle bien durante un minuto.
- Utilice un pincel o una pala para aplicar el epoxi. La vida útil es de 15 a 20 minutos a temperatura ambiente.
- El tiempo para quedar libre de pegado es de 30 minutos a temperatura ambiente. Se han obtenido excelentes resultados al curar durante 10 minutos a 100 °C. Los ciclos de curado óptimos mediante hornos de transporte radiante o de convección se determinan mejor experimentalmente. El producto también puede curarse durante 24 horas a 25 °C (77 °F).
- Limpieza/eliminación (sin curar): utilice isopropanol, acetato o MEK para limpiar la resina no curada. El revestimiento epóxico curado no se puede eliminar con disolventes.
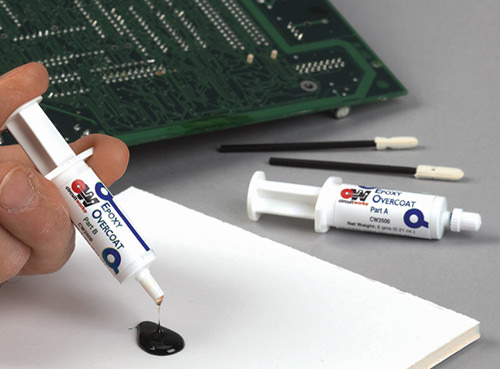
¿Qué fundente debo usar cuando reemplace los componentes de la PCB?
El fundente es necesario para prevenir la oxidación que tiende a formarse cuando los metales calientes entran en contacto con el aire. Durante la reparación y soldadura de los circuitos impresos, es frecuente ver el fundente líquido del equipo de soldadura por ola vertido en frascos y aplicado con un pincel de ácido. Esto puede provocar que se aplique demasiado fundente, obligando a realizar una limpieza adicional que de otro modo no sería necesaria. Existen otros tipos de fundente y embalajes especiales que se adaptan mejor a la reparación de las PCB:
- Rotulador de fundente: los rotuladores de fundente están precargados y cuentan con una válvula. Los rotuladores de fundente evitan el caos que implica llenar sus propias botellas de fundente. Un rotulador dispensador de fundente contiene el fundente en su tubo hermético. Los rotuladores de fundente son una excelente manera de dispensar fundente para la soldadura de mesa. Solo tiene que sostener el rotulador en posición vertical y presionar brevemente la punta para iniciar el fundente de líquido. Esto saturará la punta del rotulador con fundente. Dibuje el fundente en la zona a soldar. Presione suavemente la punta de nuevo cuando se necesite más fundente para mantener la punta húmeda con el fundente.
Los rotuladores de fundente CircuitWorks® están disponibles con diversos fundentes que se ajustan a los requisitos específicos de su negocio, como: sin limpieza, sin limpieza a alta temperatura para soldaduras sin plomo, colofonia y soluble en agua..
- Fundente pegajoso: el fundente pegajoso es una forma viscosa y pastosa de fundente que es fácil de colocar sin que se extienda a las zonas circundantes como puede hacerlo un fundente líquido. Puede utilizarse para sostener pequeñas piezas en su sitio antes de soldar y es habitual en la fabricación y reparación de componentes SMT. Los fundentes pegajosos en los dispensadores de jeringuillas proporcionan una comodidad de dispensación similar a la de un rotulador en situaciones en las que un fundente pegajoso se ajusta mejor a la aplicación. La consistencia espesa y parecida a la miel es ideal para aplicaciones de pegado de bolas, rellenado de BGA y soldadura manual de componentes SMT. El fundente se dispensa desde una jeringa y se puede extender manualmente sobre la zona que se quiera soldar.
El fundente pegajoso sin limpieza de CircuitWorks® es un fundente pegajoso sin limpieza de resina ligeramente activado (RMA). Su formulación incluye una mezcla única de resina y colofonia, junto con una mezcla patentada de activadores y estabilizadores, lo que proporciona una vida útil significativamente mayor y una estabilidad del producto a largo plazo. El residuo restante es estable y puede dejarse en una placa sin limpiar, o puede eliminarse fácilmente con el extractor de fundente sin limpieza Flux-Off® Plus. El fundente pegajoso sin plomo CircuitWorks® está formulado para temperaturas más altas, habituales en la soldadura sin plomo.
¿Hay una solución rápida para las uniones soldadas en frío?
Una unión soldada en "frío" suele ser granulada, lo que es una señal de que la soldadura no se ha fundido y mojado correctamente, por lo que puede no tener una buena unión metalúrgica. Lo más probable es que la conexión se rompa con cualquier nivel de estrés físico o térmico. Se advierte que el granulado es una señal visual para las soldaduras a base de plomo. Las soldaduras sin plomo a menudo se ven granulosas incluso cuando hay un buen enlace metalúrgico.
La forma más rápida de arreglar una unión de soldadura fría es simplemente usar un soldador para volver a fundir la soldadura. El fundente se habrá activado completamente en el proceso de soldadura original, por lo que se puede añadir un fundente adicional utilizando un rotulador de fundente CircuitWorks®.
- Presione ligeramente la punta del rotulador de fundente en la unión de la soldadura hasta que la punta se sature lo suficiente para que el fundente comience a fluir.
- Frote la punta saturada del rotulador sobre la unión soldada.
- Aplique la punta del soldador calentada a la unión soldada y vuelva a fundirla.
- Si es necesario, limpie los residuos de fundente con un hisopo saturado de un limpiador solvente como el alcohol isopropílico (IPA) o un rotulador extractor de fundente CircuitWorks.
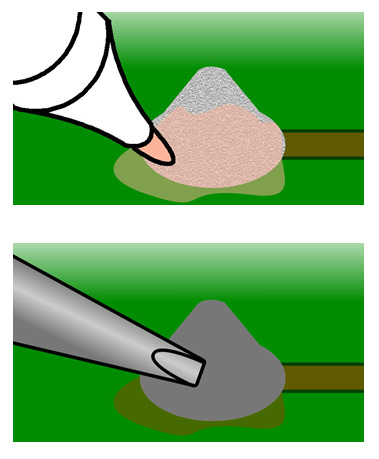
¿Cómo se reparan las almohadillas de botón conductoras de carbono negro en las PCB?
Chemtronics ofrece el kit de reparación de teclados de goma CircuitWorks®, que puede utilizarse para reparar teclados restaurando la conductividad de los contactos de carbono desgastados, intermitentes y no conductores. Es una mezcla de dos partes e incluye un hisopo, una brocha y un punzón de plástico para ayudar a mezclar y aplicar los materiales.
Para fijar las almohadillas de los botones conductores de carbono negro:
- Limpie la zona con un hisopo saturado de un limpiador de disolventes como el alcohol isopropílico (IPA) o un rotulador extractor de fundente CircuitWorks.
- Vierta el líquido de la Parte B en el recipiente de la Parte A. Remueva bien durante dos minutos.
- Pinte los contactos de carbono desgastados con el material conductor mezclado utilizando las brochas aplicadoras incluidas. Utilice la menor cantidad posible de material conductor.
- A temperatura ambiente (< 75°F / 25°C), el material se seca sin adherencias en una hora. Los teclados reparados pueden volver a ponerse en funcionamiento en 24 horas. Las propiedades finales se consiguen en 72 horas. Para lograr un secado más rápido, exponga el material a aproximadamente 190°F (90°C) durante 10 minutos. No supere los 212 °F (100°C).
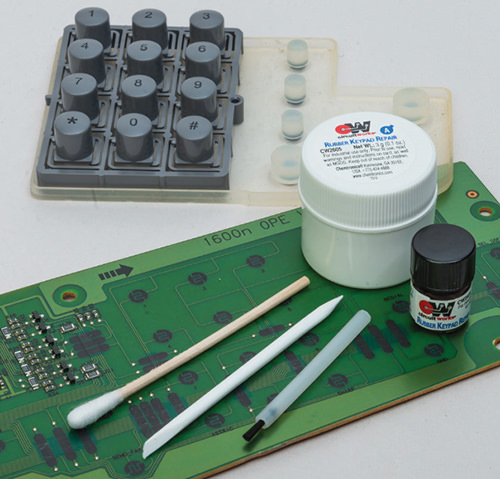
¿Hay una buena manera de eliminar las etiquetas y los residuos pegajosos?
Las viejas etiquetas de identificación o de fallos de control de calidad pueden ser difíciles de quitar. Dejan un adhesivo pegajoso que es insoluble en disolventes comunes como el alcohol isopropílico (IPA), o están tan secas y endurecidas que no se mueven. Mientras que los productos de consumo como los quitamanchas Goo Gone o bug and tar son habituales en las mesas de trabajo, Chemtronics ofrece un limpiador que en realidad está destinado a la reparación de las PCB, llamado The Mighty Pen®. Contiene un disolvente de acción rápida que descompone los adhesivos secos y pegajosos.
Cómo usar The Might Pen para quitar las etiquetas:
- Si la etiqueta es de plástico o está cubierta por una película laminada, puede que tenga que despegarla para permitir que el disolvente penetre por debajo.
- Presione ligeramente la punta del rotulador sobre la etiqueta hasta que la punta se sature lo suficiente para que el disolvente comience a fluir.
- Frote la punta saturada del rotulador sobre la zona de la etiqueta y deje que se empape.
- Deje que la etiqueta saturada se asiente durante al menos 15 o 20 segundos y luego frote la zona con la punta del rotulador hasta que se retire el material de la etiqueta y el adhesivo.
- Limpie la zona con un trapo limpio para eliminar los residuos de adhesivo y disolvente.
- Vuelva a aplicar el disolvente según sea necesario o deje un mayor tiempo de remojo para los adhesivos más resistentes.
- Si hay adhesivo acumulado en la punta del rotulador, límpiela con un trapo limpio.
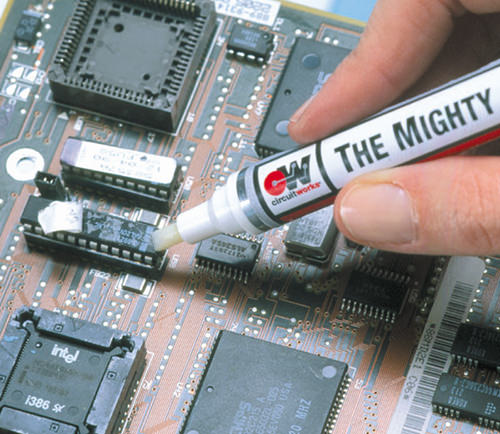
Haga una pregunta técnica
Manténgase actualizado sobre noticias, productos, videos y más de Chemtronics.