Por Grant Price, gerente de producto de Chemtronics
En realidad, ninguna operación de soldado es capaz de producir ensamblados perfectos cada vez. Incluso los componentes de la más alta calidad fallan de vez en cuando. Es por eso que el desoldado es tan importante para quienes fabrican, mantienen o reparan tarjetas de circuito impreso (PCB).
El desafío consiste en eliminar el exceso de soldadura rápidamente sin dañar la tarjeta de circuito. Por eso, en esta publicación le presentaremos nuestras mejores prácticas de desoldado, cómo usar la malla para desoldar, así como los mejores consejos que hemos recopilado a lo largo de nuestros muchos años de experiencia en la industria electrónica.
Estos consejos se centran principalmente en la eliminación de componentes con ayuda de la malla para desoldar (también conocida como alambre de soldadura o mecha desoldadora) y sus ventajas. Es portátil, fácil de usar, es una de las herramientas más comúnmente utilizadas para la reparación de la PCB y no requiere mantenimiento constante a diferencia de otras herramientas.
1. Mantenga La Punta de Su Soldador Limpia Y Estañada Para Una Conducción Efectiva Del Calor
Aunque podría parecer obvio, esto es algo que a menudo se pasa por alto y es crítico para un desoldado eficiente. Las puntas del soldador cubiertas con flux quemado y óxido no se humedecerán (captarán la soldadura) y serán malas conductoras de calor. Una punta de soldador limpia y estañada conduce mejor el calor a través de la malla para desoldar e inicia la acción de absorción más rápidamente.
- Antes de iniciar, estañe la punta del soldador, agregándole nuevo alambre de soldadura.
- Si la punta del soldador no responde a la soldadura adicional, reactive las puntas sucias usando un limpiador de puntas, a menudo denominado "estañador de puntas". El estañador de puntas de la marca Plato (número de catálogo # TT-95) es una pasta sólida, libre de haluros, que proporciona un re-estañado y una limpieza rápida y segura de las puntas oxidadas. Haga rodar la punta caliente en el compuesto hasta que el estañado brillante rodee el extremo de la punta.
- Elimine cualquier compuesto residual de la punta aplicando alambre de soldadura y a continuación limpie con una esponja húmeda o un limpiador de punta de alambre de latón.
- Finalmente, aplique nuevamente soldadura a la punta para protegerla de la oxidación.
Cuando su soldador haya permanecido en reposo por un período de tiempo prolongado, o después de que haya terminado de soldar, “estañe” la punta de soldadura con soldadura nueva para evitar la oxidación.
2. Minimice El Tiempo Durante El Cual La Tarjeta Y Los Componentes Permanecen A Una Temperatura Elevada
La aplicación de altos niveles de calor a la tarjeta o sus componentes durante un período prolongado puede dañar su tarjeta, sus componentes, crear uniones soldadas frágiles y provocar problemas de funcionamiento a lo largo del proceso.
- Mantenga su soldadura a una temperatura razonable. Aunque puede resultar tentador subir la temperatura del soldador al máximo para aumentar la eficiencia, hacerlo podría afectar a los componentes. Incluso con soldaduras sin plomo, cualquier temperatura por encima de 700 ºF (371 ºC) implica un riesgo de daño a los componentes por tensión térmica. Si considera que es necesario seguir aumentando la temperatura a lo largo del día, consulte el consejo #1.
- En el caso de que haya varios componentes para reemplazar en un solo conjunto o los componentes sean particularmente sensibles al calor, puede usar un precalentador de la PCB. Los precalentadores le permiten aumentar la temperatura de la tarjeta y mantener dicha temperatura mientras realiza su trabajo. Aunque la temperatura de precalentamiento estará muy por debajo del punto de fusión de la soldadura, el choque térmico a los componentes se minimiza porque ésta no aumenta rápidamente desde la temperatura ambiente.
3. Haga Coincidir El Ancho de La Malla Con La Unión Soldada O La Almohadilla de Contacto
La malla para desoldar viene normalmente en diferentes anchos, de manera que pueda acoplarse a lo que está desoldando. Las mallas que son demasiado delgadas no eliminarán suficiente soldadura y requieren que recorte y vuelva a fundir la soldadura repetidamente. Las mallas que son demasiado anchas tardan más en calentarse y pueden interferir con otros componentes en la tarjeta de circuito.
Seleccione el ancho de malla para desoldar que mejor coincida con el tamaño del área de contacto. Esto asegurará que obtenga una conducción de calor adecuada y que no desolde las áreas no deseadas. Los anchos del alambre de soldadura se designan con los números 1 a 6 o códigos de color, que son los estándares en la industria.
- La malla #1/blanca es la más pequeña (menos de 1 mm de ancho) y se usa principalmente para SMD y microcircuitos.
- Muchos consideran que #2/amarillo, #3/verde y # 4/azul son los alambres de desoldado más comunes.
- La malla #5/café es ideal para eliminar grandes gotas de soldadura y la malla #6/roja es más adecuada para desoldar almohadillas o terminales BGA.
- Mantenga tres o cuatro anchos diferentes en su área de trabajo para abarcar todos los casos.
- La malla se puede plegar o recortar en ángulo para adaptarse mejor al área de contacto.
4. Haga Que La Punta del Soldador Coincida Con El Ancho de La Malla Para Una Mayor Precisión
Use una punta de soldadura que tenga aproximadamente el ancho de la malla y el área de contacto. Una punta que es demasiado pequeña requerirá más tiempo, mientras que una punta demasiado grande corre el riesgo de exponer otros componentes en un ensamblaje denso. Hacer coincidir la punta le permite derretir la soldadura no deseada más rápido y minimiza el tiempo de aplicación de calor. Use la punta de una navaja o cuchillo cuando desolde áreas grandes, como una almohadilla BGA.
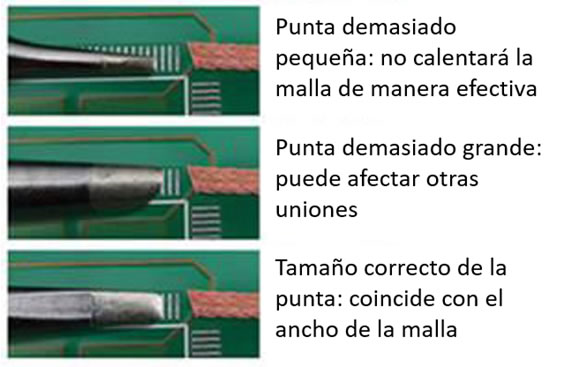
5. Precaución: Al Arrastrar La Desoldadura, Desplace La Punta Sobre La Malla Y No La Malla A Través de Las Almohadillas
Al arrastrar la malla de cobre sobre las almohadillas, por ejemplo, al desoldar las almohadillas BGA, se puede rayar el revestimiento de OSP e incluso las almohadillas mismas si se aplica suficiente presión. Por lo tanto, es más conveniente aplicar la malla y posteriormente arrastrar la punta del soldador sobre la misma.
6. Recorte La Malla Para Desoldar Usada Después de Cada Utilización
Aunque resulta tentador desoldar un área y seguir subiendo el carrete de la malla, es más adecuado trabajar hacia el final de la malla para aislar el calor. Una vez que la malla para desoldar alcanza la temperatura de soldadura, el flux se activa por completo, por lo que esa parte no atraerá más soldadura. Las hebras largas de malla usada solo actúan como disipadores de calor, lo que hace más lento el proceso.
7. Evite El Error De Novatos #1: Levantar El Soldador Y Malla Al Mismo Tiempo
Este es el error más común cometido por operadores sin experiencia. Después de quitar la soldadura, asegúrese de levantar el soldador y malla al mismo tiempo. De lo contrario, soldará la malla al contacto y correrá el riesgo de levantar la almohadilla.
8. Haga Coincidir El Tipo de Flux Con Su Proceso de Limpieza
La malla para desoldar está disponible en varios tipos de flux dependiendo de su proceso de limpieza y otros requisitos.
- Colofonia – La malla para desoldar de flux de resina tiene la acción de absorción más rápida, pero deja residuos que deben limpiarse a fondo.
- No-Clean – La malla de flux sin limpieza es ideal cuando la limpieza es poco práctica o imposible de realizar. Después de desoldar, lo único que queda es un residuo claro, no iónico. Es el tipo de malla a utilizar para el trabajo de campo, cuando una limpieza a fondo es más complicada.
- Unfluxed – Puede agregar su propio flux a este tipo de malla en un entorno de producción o reparación donde se especifica el flux y no es posible modificar el mismo, o cuando se requiere un flux acuoso. La malla sin flux no eliminará la soldadura a menos que se agregue flux. Hay diferentes tipos de fluxs disponibles en presentación tipo lápiz, lo cual es ideal para la malla.
9. Elija La Presentación Disipativa Estática Para Aplicaciones Estáticas Sensibles
Cuando trabaje con ensamblajes sensibles a la electricidad estática, asegúrese de que el carrete de la malla desoldadora sea disipador de estática (o que sea seguro contra descargas electrostáticas). Hemos visto casos en los que un operador cuenta con la estación de trabajo más costosa y con seguridad contra descargas electrostáticas, así como una alfombrilla y tiras de puesta a tierra de alta seguridad, pero se descubre que está usando un carrete aislante. La mayoría de las presentaciones de malla disipativa se pueden identificar por su color azul. Incluso si un carrete es negro, no asuma que cumple con el S20.20.
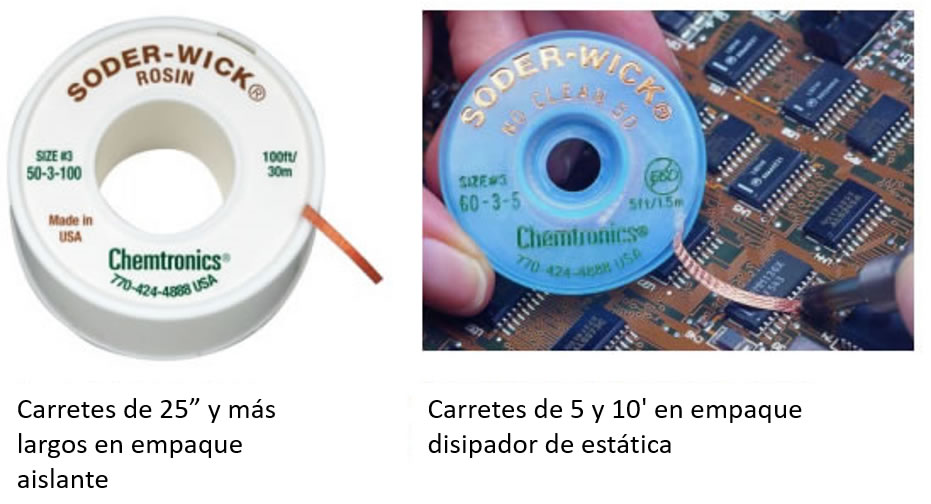
10. Agregar Soldadura A Áreas Estrechas En Realidad Facilita Su Eliminación
Aunque puede ser difícil eliminar las cantidades pequeñas de soldadura en fisuras estrechas, las uniones soldadas más grandes y uniformes se absorben de inmediato. Por contradictorio que parezca, resulta de gran utilidad agregar más soldadura a uniones como ésta antes de absorber la soldadura no deseada.
11. Proteja Su Tarjeta Contra La Corrosión Utilizando Un Removedor de Flux de Calidad
Los residuos de flux pueden causar crecimiento dendrítico y corrosión en los conjuntos de la PCB, así que asegúrese de utilizar las mejores prácticas y limpie la tarjeta. Después de reemplazar todos los componentes y eliminar el exceso de soldadura, realice lo siguiente:
- Limpie el área a fondo con un removedor de flux de calidad
- Incline la tarjeta para permitir que el limpiador y los residuos se escurran
- Si es necesario, use un cepillo de pelo de caballo o una toallita sin pelusa para frotar suavemente la PCB, y a continuación, enjuague la tarjeta.
- Si usa una toallita, asegúrese de que no deje fibras/pelusas en su PCB, ya que esto puede causar problemas más adelante.
Este es un paso opcional para una malla sin limpieza, pero sigue siendo una buena idea para tarjetas densamente pobladas o de alto voltaje. Este paso es absolutamente necesario, independientemente del tipo de flux, si planea continuar su reparación con un revestimiento de conformal.
12. Siga Nuestro Proceso de Desoldado Recomendado Para Obtener Los Mejores Resultados
Por último, nos gustaría terminar esta publicación explicando cómo usar la malla para desoldar.
- Coloque la malla sobre la soldadura no deseada, preferiblemente en la mayor acumulación de soldadura para que maximice el contacto de la malla con el área de la superficie de la soldadura.
- A continuación, coloque la punta del soldador sobre la malla a 45 grados y permita que el calor se transfiera a la almohadilla. La malla absorberá la soldadura fundida.
- Desplace la punta y la malla para desoldar según sea necesario para eliminar toda la soldadura al mismo tiempo. Tenga cuidado de no arrastrar la malla sobre las almohadillas, ya que se pueden rayar.
- Una vez que la malla esté llena de soldadura, debe recortar la porción gastada y pasar a una malla nueva para extraer más soldadura. Retire el soldador y la malla simultáneamente para evitar soldar el cable a la tarjeta.
Eso es todo. Al seguir estos consejos, estará utilizando las mejores prácticas probadas en la industria para la eliminación eficiente de la soldadura. Y ahora nos gustaría conocer su opinión. ¿Qué le pareció nuestra lista? ¿Omitimos algún consejo importante? Asegúrese de publicar sus preguntas y comentarios a continuación. Póngase en contacto con nosotros si necesita ayuda para seleccionar la mejor malla desoldadora para su aplicación.
Haga una pregunta técnica
Manténgase actualizado sobre noticias, productos, videos y más de Chemtronics.