En el proceso de montaje, repaso o reparación de placas de circuitos impresos (PCB) para dispositivos electrónicos, la cuestión se centra inevitablemente en si se debe limpiar o no la PCB. La limpieza supone más tiempo y gastos para el proceso, y hacerlo mal puede causar más daño que bien. Esta guía le explicará las razones para limpiar las PCB y las mejores prácticas para la limpieza de los componentes electrónicos.
¿Por qué limpiar una placa de circuitos impresos (PCB)?
Dado que la limpieza de las PCB no siempre es necesaria y añade tiempo y gastos al proceso de producción o reparación, puede ser necesaria alguna justificación.
Mejorar la apariencia estética de la PCB
Si es un fabricante contratista de PCB, el aspecto visual de la placa se refleja en su trabajo. Un residuo claro y grasiento alrededor de una junta de soldadura puede hacer que salten las alarmas para los inspectores de control de calidad de su cliente. Si el residuo de fundente se carboniza y forma puntos en las uniones de soldadura, puede parecer un defecto real, como un vacío o un "agujero de soplado" de la unión de soldadura. Si el residuo de fundente proviene de un proceso de repaso, actúa como señal de fallo en la zona de repaso, llamando la atención sobre el trabajo, incluso si no debería ser motivo de preocupación.
Mejorar la confiabilidad de la PCB
Los requisitos de confiabilidad generalmente están determinados por la naturaleza del producto final. En el caso de un producto desechable como el teclado de una computadora, no pasa nada si deja de funcionar. En ese caso, un proveedor de servicios de emergencia puede utilizar un fundente sin limpieza y renunciar al proceso de limpieza. En el otro lado de la balanza, los requisitos para los componentes electrónicos de los marcapasos, donde el fallo de la placa podría provocar directamente la muerte, serán mucho más estrictos. En ese ejemplo, se exigirá la limpieza después del montaje y de cualquier repaso posterior, y el proceso se someterá a pruebas exhaustivas de eficacia y reproducibilidad. Los bienes duraderos de larga duración pueden quedar en algún punto intermedio, siendo la limpieza un requisito, pero sin pruebas y controles rígidos.
Evitar la corrosión de los componentes y la PCB
Los residuos de fundente que quedan en los circuitos electrónicos son ácidos. Si no se eliminan mediante un proceso de limpieza, pueden absorber la humedad ambiental del aire y provocar la corrosión de los cables de los componentes y los contactos de la PCB.
Corrosión en el ensamblaje fallido en la zona de QFP (foto cortesía de Foresite)
Evitar los problemas de adherencia con el revestimiento de conformación
La mayoría de la gente entiende que cuando se pinta algo, la superficie debe estar preparada para que quede absolutamente limpia. De lo contrario, la pintura se levantará rápidamente de la superficie y se desprenderá. La misma lógica se aplica a la capa de conformación, incluso cuando la contaminación es de fundente sin limpiar. "Sin limpiar" se refiere a la cantidad de material iónico que queda después de la soldadura. No tiene nada que ver con si el revestimiento puede adherirse o no.
Cuando quedan residuos de fundente en la PCB antes del proceso de revestimiento, es frecuente ver que el revestimiento se levanta o se despega de la superficie de la placa. Esto es evidente cuando las bolsas están aisladas alrededor de las uniones de soldadura en lugar de la superficie general (la excepción es la parte inferior de una soldadura de onda de la PCB).
Para colmo, los revestimientos son por lo general semipermeables, por lo que permiten respirar hasta cierto punto. La humedad puede entrar y empapar el residuo de fundente, y esto puede provocar corrosión.
Residuos de fundente que causan el levantamiento de la capa (foto cortesía de NPL)
Prevenir el crecimiento dendrítico de la contaminación iónica
Las partículas polares o iónicas que quedan de los residuos de fundente y otras fuentes, cuando se exponen a la humedad del aire ambiente y cuando se aplica la corriente, pueden enlazarse en una cadena o rama llamada dendrita (fig. 1). Estas dendritas son conductoras, por lo que forman un rastro no intencional que causa fugas de corriente o, durante un largo periodo de tiempo, incluso un cortocircuito.
Fig 1 – formación de dendritas
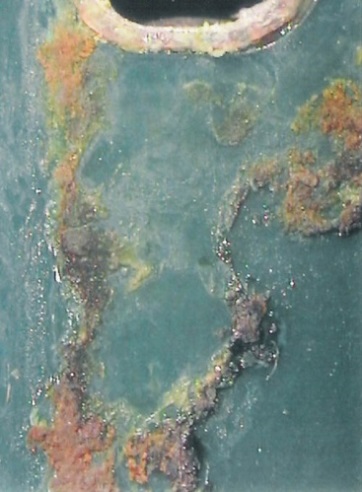
Crecimiento dendrítico entre las almohadillas de soldadura, causado por la contaminación iónica (fotos cortesía de Foresite)
¿Qué es la contaminación iónica?
¿Qué es la contaminación polar?
Los contaminantes iónicos son restos de fundente que quedan durante el proceso de ensamblaje. Los compuestos iónicos se mantienen unidos por fuerzas electrostáticas y el propio compuesto tiene una carga neta cero. Estos materiales se disocian cuando se exponen al agua. Están compuestos de cationes, cargados positivamente, y aniones, cargados negativamente. Un ejemplo sencillo es la sal de mesa (cloruro de sodio), compuesta por un único catión de sodio, positivo, que carece de un electrón, y un anión de cloruro, con carga negativa (Cl), que tiene un electrón extra. Los compuestos polares, por otra parte, pueden tener una carga positiva en un lado de la molécula y una carga negativa en el otro lado de la molécula; estas moléculas nunca se separan. El agua, el isopropanol (o IPA) es un ejemplo de una molécula polar.
Al rellenar la placa de componentes, los propios componentes también pueden transportar varios contaminantes iónicos/conductores a su montaje, entre los que se incluyen aceites/fluidos de corte, biocidas y productos anticorrosivos. Tenga en cuenta los materiales no iónicos comunes que también pueden afectar a los pasos de montaje: aceites de procesado, liberación de moho, etc. y que pueden ser perjudiciales en el futuro.
¿Cuáles son los contaminantes iónicos más comunes en la fabricación de las placas sin revestimiento?
La humedad común atrapada en el proceso de "estratificación"
El agua es un contaminante polar. Es propicia para la disociación de otros materiales iónicos, lo que sienta las bases para los accidentes de conducción (crecimiento dendrítico, ECM, etc.). Es una práctica común "organizar por lotes" las placas para eliminar la humedad exterior.Corrosión por contaminación de fabricación de PCB (foto cortesía de Foresite)
Productos químicos de grabadoEstos son altamente conductores y también pueden ser corrosivos. Deben ser neutralizados químicamente y retirados/enjuagados y se sabe que son causa de pérdidas de corriente.
Residuos de fundente de la soldadura
Residuo pesado de fundente sin limpiar con corrosión visible de cobre (foto cortesía de Foresite)
Todo el mundo está familiarizado con los residuos de fundente. Los fundentes, ya sea en forma líquida, en alambre con núcleo o en forma de pasta, pueden dejar residuos que pueden causar serios defectos de fiabilidad si no se eliminan. Los residuos de fundentes conductores habituales del proceso de soldadura pueden incluir varios activadores, aglutinantes, componentes reológicos y saponificadores que no han reaccionado. Entre ellos hay numerosas iteraciones de ácidos (abiéticos, adípicos, succínicos, entre otros), ingredientes muy básicos (compuestos amino) e incluso componentes que se encuentran en los "jabones" como los iones fosfato y sulfato. Todos ellos se deben limpiar del sustrato, ya sea mediante una estricta limpieza con disolventes, como el desengrasado con vapor, o mediante productos químicos acuosos utilizados habitualmente en los limpiadores por lotes o por líneas que se ven en el piso de la fábrica.
Residuos entre capas de los procesos de perforación y enchapado
Crecimiento dendrítico entre las almohadillas de soldadura, causado por la contaminación iónica (foto cortesía de Foresite)
Además de estos residuos que se ven con frecuencia, también hay que eliminar los residuos de la propia química del proceso de limpieza. Esto se nota más en los sistemas de limpieza acuosos. Muchos utilizan saponificadores para neutralizar y emulsionar los residuos de fundente y hacerlos más fáciles de enjuagar/eliminar del sustrato. Estos componentes en sí mismos son altamente polares e iónicos y también pueden mejorar la dendrita o el mecanismo ECM si no se eliminan. Además, en estos productos se suelen utilizar preventivos de la corrosión y agentes tensoactivos. Esto no es algo malo en sí mismo, pero hay que tener cuidado para asegurar que se eliminan junto con los sustratos durante el proceso de limpieza.
¿Cómo se realizan las pruebas de contaminación iónica?
Un control de calidad deficiente desde la fabricación de las PCB, hasta la soldadura y la dotación de componentes, y las etapas de limpieza final, son fuentes potenciales de contaminación. Muchas de estas pueden localizarse mediante pruebas y análisis de contaminación iónica, como las pruebas ROSE, la extracción de iones y la cromatografía, así como durante las pruebas iniciales de validación de humedad elevada al comienzo del proyecto.
Un control de calidad estricto y procedimientos operativos estándar durante el montaje de las PCB y las etapas de fabricación del montaje y las pruebas de validación pueden contribuir en gran medida a evitar una auténtica catástrofe en términos de confiabilidad. Piénselo: la simple manipulación incorrecta de una pieza por parte de un operario que no use guantes puede trasladar sales y aceites de la piel al sustrato, ¡lo que podría ser potencialmente catastrófico para su artículo!
¿Qué es el residuo blanco en una placa de circuitos electrónicos?
El residuo blanco suele ser un síntoma de la ineficacia en la limpieza de las PCB. Los residuos de fundente conductor comunes del proceso de soldadura pueden incluir varios activadores, aglutinantes, componentes reológicos y saponificadores que no han reaccionado. Entre ellos hay numerosas iteraciones de ácidos (abiéticos, adípicos, succínicos, entre otros), ingredientes muy básicos (compuestos amino) e incluso componentes que se encuentran en los "jabones", como los iones fosfato y sulfato. Cuando un limpiador no disuelve completamente todos los constituyentes, o no se permite que el limpiador salga de la PCB, el disolvente restante puede evaporarse y dejar residuos que son blancos o como manchas de agua.
Residuo de fundente blanco con corrosión de cobre visible (foto cortesía de Foresite)
¿Cómo se eliminan los residuos blancos de una placa de circuito electrónico?
Los residuos blancos por lo general se pueden limpiar con un eliminador de fundente. Si los residuos son el resultado de una solvencia insuficiente del proceso de limpieza original, puede ser necesario un limpiador de solvente más fuerte. A menudo es necesario agitar para eliminar los residuos, lo que puede hacerse con una toallita, un hisopo, un cepillo o un aerosol con un accesorio de cepillo. Siga estos pasos para eliminar los residuos blancos:
- Rocíe el residuo con un disolvente fuerte.
- Mientras la zona esté todavía húmeda, frote con una herramienta limpia como una bayeta, un hisopo o un cepillo.
- Rocíe la zona limpiada y las zonas circundantes con el mismo disolvente, inclinando la placa para que el aclarado pueda salir.
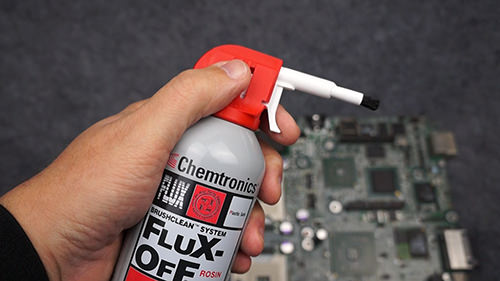
Resina Flux-Off® con un accesorio de cepillo
¿Cuáles son los diferentes métodos de limpieza de las placas de circuitos electrónicos?
La extracción del fundente de la PCB puede realizarse en la mesa de trabajo, lo que generalmente exige un método de limpieza manual. Esto es frecuente para el ensamblaje, el paso y la reparación de PCB electrónicas de bajo volumen. Los métodos de limpieza manual suelen ser más laboriosos y menos repetitivos, por lo que los resultados pueden variar de un operador a otro. En el caso de un montaje de mayor volumen o de menor variabilidad, se utilizan métodos de limpieza más automatizados.
Métodos manuales de extracción de fundente
- Aerosol: los extractores de fundente de aerosol tienen la ventaja de contar con un sistema sellado, que garantiza un solvente fresco cada vez, y la agitación que proporcionan la presión y el patrón de pulverización. Generalmente se incluye un accesorio de paja para pulverizar en las zonas con mayor precisión.
- Aerosol con accesorio de cepillo: se puede añadir un cepillo a la boquilla del aerosol, de manera que el disolvente se rocía a través del cepillo mientras se friega.
- Rociado con disparador: las botellas de rociado con disparador son más comunes para los limpiadores a base de agua y alcohol isopropílico (IPA), pero no para los limpiadores solventes agresivos.
- Inmersión líquida: la PCB puede sumergirse en una bandeja o cubo de limpiador con disolvente, con herramientas de limpieza como hisopos y cepillos, que se utilizan según sea necesario para sustratos resistentes. El rendimiento de la limpieza puede mejorarse aún más calentando el disolvente, pero esto solo debe hacerse con extractores de fundente no inflamables.
- Limpieza de manchas con un hisopo: un hisopo de algodón o de espuma puede saturarse con un disolvente suave como el alcohol isopropílico, a menudo de un dispensador de bomba o "dauber".
- Trapos y paños presaturados: para mayor comodidad, existen trapos y paños presaturados con un disolvente suave como el alcohol isopropílico.
Métodos automatizados o semiautomáticos de extracción de fundente
- Ultrasonidos: los equipos de limpieza por ultrasonido utilizan ondas de sonido para crear implosiones dentro del residuo de fundente, rompiéndolo y levantándolo de la PCB. La mayoría de los equipos tienen la opción de calentar el disolvente para aumentar el rendimiento de la limpieza. Use esta opción solo con un extractor de fundente no inflamable. La contaminación cruzada puede ser un problema, así que cambie el disolvente con regularidad. La limpieza ultrasónica podría ser demasiado brusca en componentes sensibles como las resistencias de base cerámica.
- Desengrasante de vapor: el desengrasante de vapor es el proceso de limpieza de mayor precisión, como el que se usa en los componentes electrónicos aeroespaciales y médicos. Las PCB pueden sumergirse en un sumidero de disolvente hirviendo, en un sumidero de enjuague con ultrasonidos y enjuagarse en vapores de disolvente. Es necesario utilizar disolventes especiales que son azeotrópicos o casi azeotrópicos, de modo que no cambien al hervir los disolventes y reconstruirlos en un ciclo continuo.
- Extractor de fundente por lotes: básicamente un lavaplatos para placas de circuitos electrónicos. La PCB se mantiene en su sitio mientras la máquina pasa por el ciclo de lavado, enjuague y finalmente secado.
- Extractor de fundente en línea: un lavador en línea es algo parecido a un túnel de lavado para placas de circuitos electrónicos. Las PCB se desplazan en una cinta transportadora a través de las zonas de lavado, enjuague y secado. Se utilizan extractores de fundente a base de agua.
¿Afecta el tipo de fundente a la eficacia del proceso de limpieza de las PCB?
El tipo de fundente puede tener un gran impacto en el proceso de limpieza. Los fundentes R, RA y RMA son por lo general más fáciles de eliminar con extractores de fundente estándar y alcohol isopropílico. Los fundentes sin limpiar están destinados a permanecer en la PCB, por lo que pueden ser más difíciles de eliminar. Pueden ser necesarios un extractor de fundente de disolvente más agresivo, una agitación adicional como el cepillado o un disolvente calentado. Los fundentes acuosos normalmente están diseñados para su extracción en un sistema de limpieza por lotes o en línea con agua desionizada directa o agua con un saponificador. También se pueden utilizar disolventes con base de alcohol o especialmente formulados para limpiar los fundentes acuosos, pero los mismos limpiadores pueden tener resultados mixtos en otros tipos de fundentes.
La respuesta corta es hacer coincidir el extractor de fundente con el tipo de fundente. Esto puede ser un reto para un fabricante de componentes electrónicos que puede tener que utilizar diversos fundentes según lo requieran sus distintos clientes. Existen extractores de fundente que pueden descomponer una gran variedad de fundentes, y el cambio de variables como el tiempo de limpieza, la agitación y el calor adicional puede marcar la diferencia.
En el caso de los limpiadores a base de agua que funcionan en un sistema de limpieza por lotes o en línea, se puede ajustar la concentración del limpiador, aumentar el tiempo de ciclo y la temperatura para mejorar el rendimiento.
¿Qué factores causan la dificultad de limpiar los residuos de fundente de las PCB?
Cualquier ingeniero de procesos le dirá que la clave para diseñar un proceso repetible es controlar las variables. Al eliminar el fundente de las placas de circuitos electrónicos, hay una serie de variables que pueden cambiar drásticamente el rendimiento de limpieza de un proceso:
- Tipo de fundente: el tipo de fundente puede tener un gran efecto en el proceso de limpieza. Los fundentes R, RA y RMA son por lo general más fáciles de eliminar con extractores de fundente estándar y alcohol isopropílico. Los fundentes sin limpiar están destinados a permanecer en la PCB, por lo que pueden ser más difíciles de eliminar. Pueden necesitar un extractor de fundente más agresivo, agitación adicional como el cepillado o un disolvente calentado. Los fundentes acuosos están generalmente diseñados para eliminarse mediante un sistema de limpieza en línea o por lotes con agua desionizada directa o agua con un saponificador. También se pueden utilizar disolventes con base de alcohol o especialmente formulados para limpiar los fundentes acuosos, pero los mismos limpiadores pueden tener resultados mixtos en otros tipos de fundentes.
- Fundentes de alto contenido en sólidos: la limpieza de una PCB hecha con una mezcla de tecnologías de soldadura puede ser especialmente difícil. Los fundentes pegajosos u otros tipos con un alto nivel de sólidos pueden ser más difíciles de limpiar, requieren más tiempo de limpieza, tiempo de remojo o agitación adicional.
- Cantidad de fundente: una capa más gruesa de residuo de fundente supone más suciedad para eliminar, y puede crear presas de fundente bajo componentes de bajo nivel de separación. Esto evita que el extractor de fundente penetre completamente bajo el componente.
- Temperatura de soldadura: las temperaturas más altas tienen una mayor tendencia a endurecer los residuos de fundente, haciéndolos más difíciles de eliminar. La soldadura a altas temperaturas puede exigir más tiempo de limpieza, tiempo de inmersión o agitación adicional.
- Soldadura sin plomo: la soldadura sin plomo por lo general requiere una temperatura de soldadura más alta y unos fundentes más altamente activados. Los residuos de fundente que quedan de un proceso de soldadura sin plomo pueden exigir un mayor tiempo de limpieza, tiempo de inmersión o agitación adicional, y puede que tenga que plantearse un extractor de fundente más agresivo que esté diseñado para procesos sin plomo.
- Tiempo entre la soldadura y el proceso de limpieza: no es inusual terminar el ensamblaje el viernes, volver el lunes para limpiar y que le sorprendan residuos de fundente blanco. A medida que los residuos de fundente se asientan en la PCB, los elementos volátiles continúan saliendo y se vuelven más difíciles de eliminar.
¿Cómo se limpia una PCB después de soldar?
¿Cómo se elimina el fundente de la soldadura?
La forma más común de limpiar los residuos de fundente de una zona de reparación es saturar un trapo de algodón o de espuma con alcohol isopropílico u otro disolvente de limpieza, y frotarlo alrededor de la zona de reparación. Aunque esto puede ser adecuado para el fundente sin limpiar, cuando el objetivo es una PCB visualmente limpia, puede no ser lo suficientemente limpio cuando se trata de fundentes más fuertemente activados, como RA o acuosos. El pequeño secreto es que los residuos de fundente no se evaporarán junto con el disolvente. Puede disolver el fundente, y algunos de los residuos se empaparán en el trapo, pero la mayoría de los residuos se asentarán de nuevo en la superficie de la placa. Muchas veces estos residuos blancos son más difíciles de eliminar que el fundente original.
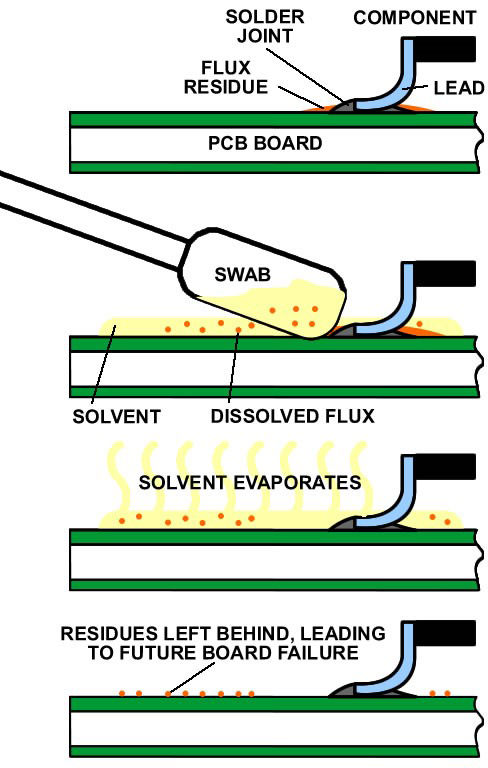
Los residuos de fundente no se evaporan junto con el disolvente.
Una mejora rápida y fácil de este proceso es enjuagar la placa después de limpiar la zona de reparación. Mientras el disolvente está todavía húmedo, pulverice toda la placa con un limpiador de flujo en aerosol. Sostenga la PCB en un ángulo para permitir que el disolvente fluya sobre la placa y se escurra, junto con cualquier residuo que se recoja.
El accesorio de paja que acompaña a los limpiadores de fundente en aerosol es una buena manera de aumentar la capacidad de pulverización y de penetrar bajo los componentes.El aerosol con paja sirve para limpiar los componentes inferiores
Chemtronics ofrece el sistema BrushClean™ con muchos de sus extractores de flujo. El disolvente limpiador se rocía a través del cepillo, por lo que la agitación se puede aumentar restregando mientras se rocía. Para absorber los residuos de fundente, se puede colocar un limpiador de policelulosa sin pelusa sobre el área de reparación y se puede pulverizar y frotar el material. Luego se retira el accesorio de limpieza y cepillado, y se rocía sobre la placa para el enjuague final.
El accesorio de cepillo de aerosol sobre un rascador se disuelve y absorbe los residuos de fundente al mismo tiempo.
¿Cómo utilizo el accesorio de paja en el extractor de flujo de aerosol para mejorar la eficacia de la limpieza?
El uso del accesorio de paja permitió un rociado más controlado, eliminando así el excesivo desperdicio de disolvente. La paja también era útil para dirigir exactamente donde iba el disolvente. Esto permitió al usuario guiar el disolvente bajo el componente. Sin el accesorio de la paja, el disolvente se pulverizaba en la zona del objetivo (por ejemplo, los lados del componente); sin embargo, gran parte del material se desperdiciaba en las zonas que rodeaban el objetivo y muy poco terminaba pasando por debajo del componente (vea la figura 1).
Figura 1: Comparación visual de un aerosol sin (izquierda) y con un accesorio de paja.
¿Cómo puedo limpiar los componentes inferiores con un extractor de fundente de aerosol?
Los mejores resultados se obtuvieron cuando se trataron tanto las esquinas como los lados de cada componente contaminado, en lugar de centrarse solo en una cosa, esquinas o lados. Dirigir el disolvente directamente a las esquinas ayudó a romper cualquier depósito de fundente que estuviera situado allí. Como las esquinas se despejaron primero cuando se abordaron los lados de los componentes, el número de canales abiertos para permitir el paso del disolvente fue mayor que cuando las esquinas no se trataron primero. Cuantos más canales abiertos haya disponibles, mayores serán las posibilidades de que el fundente quede expuesto al disolvente y, por consiguiente, mayores serán las probabilidades de que todo el fundente atrapado bajo el componente pueda salir de él.
La elección de utilizar un rocío oscilante o estacionario dependía del tamaño del componente. En el caso de un componente pequeño, bastaba con utilizar un rociador estacionario en los lados del componente; sin embargo, en el caso de los componentes más grandes, se lograba una mayor limpieza de la placa cuando el rociador oscilaba de un lado a otro del componente. Este rocío oscilante daba al disolvente la oportunidad de fluir hacia arriba, debajo del componente desde muchos ángulos, de forma similar a como lo hacía el fundente.
¿Afecta el ángulo del aerosol a la eficacia de la limpieza cuando se usa un extractor de fundente en aerosol?
En nuestras pruebas, un ángulo de paja exacto de 30º, 45º o 60º con respecto a la placa no tuvo ningún impacto en la limpieza de la misma. Los ángulos generales hacia abajo o hacia arriba fueron suficientes. Para aprovechar al máximo la paja, piense en la dirección en la que deben desplazarse los residuos. Al tratar de eliminar los residuos de debajo de un componente, rocíe cerca de la placa en un ángulo que guíe el disolvente bajo el componente. Cuando todos los residuos se hayan eliminado de debajo del componente, rocíe desde la parte superior del componente, con un ángulo a lo largo de los bordes para empujar cualquier residuo hacia fuera, lejos del componente.
¿Existen maneras correctas e incorrectas de usar las herramientas de limpieza como los cepillos, los paños y los trapos?
Los cepillos y trapos de mano dejaban la placa más sucia de lo que estaba. Los cepillos y trapos esparcían un fundente parcialmente disuelto alrededor de los componentes que luego se secaba, dejando un residuo blanco. Ninguno de los paños de espuma de poliuretano se sostuvo bien en esta aplicación. Los trapos de espuma se volvían endebles cuando se saturaban de solventes agresivos y se rompían fácilmente. Otro problema con las herramientas de mano era que el disolvente se evaporaba demasiado rápido. Los mejores resultados se lograban cuando se utilizaba un enjuague final (consulte figura 2). La clave es no dejar que la placa se seque. Cuando la placa se seca, el fundente parcialmente disuelto se seca, dejando el residuo blanco mencionado anteriormente. Un disolvente de evaporación más lenta, como el IPA, evitaría el problema de la evaporación pero debería ir seguido de un enjuague (consulte más detalles sobre el enjuague a continuación). Además, algunos disolventes pueden desplazarse bajo el componente durante el frotado, pero sin la aplicación de la fuerza de un aerosol, la probabilidad de que los residuos bajo el componente sean expulsados es escasa.
Figura 2: La placa se limpió con un cepillo de mano. Se humedecieron los componentes y luego se mojó el cepillo y se utilizó para fregar la zona contaminada. La placa de la primera foto no se enjuagó por última vez. La placa de la segunda foto sí lo hizo (Nota: no se eliminó todo el fundente).
Algunos limpiadores solventes incluyen un cepillo que se fija directamente al cabezal de pulverización, y el solvente fluye a través del cepillo a un ritmo lento (consulte la figura 3). Esto es particularmente frecuente en los defluxores disponibles en Europa. Los accesorios de cepillo produjeron resultados que estaban un paso por encima de las herramientas de mano, debido al beneficio de un suministro constante de disolvente virgen. Sin embargo, no produjeron el mismo nivel de limpieza que se observa en la limpieza con solo aerosol. El accesorio de cepillo permitió restregar las zonas problemáticas, lo que puede ser beneficioso. Sin embargo, la fuerza de un aerosol a través de un accesorio de paja produjo resultados similares.
Los accesorios de los cepillos, como las herramientas de mano, pueden introducir nuevos contaminantes. Además, para que un accesorio de cepillo alcance su máximo potencial, se necesita un aerosol independiente para la limpieza debajo de los componentes y para el enjuague final. Al igual que las herramientas de mano, sin la fuerza de un aerosol, algún disolvente puede pasar por debajo del componente durante el fregado; no obstante, la probabilidad de que los residuos bajo el componente sean expulsados es escasa. Dado que el uso de un accesorio de cepillo requiere que la zona objetivo permanezca saturada, esta permanece en una piscina de disolvente durante todo el periodo de limpieza. Esto aumenta la probabilidad de que los residuos solo se puedan reubicar en la placa en lugar de ser eliminados por completo. Por lo tanto, se consideró que un enjuague final era especialmente importante para asegurar que todos los residuos se eliminaran de la placa (consulte las figuras 4 y 5).
Existe un sistema de cepillos disponible en el mercado que proporciona un mecanismo de cepillo independiente para la limpieza, que recibe continuamente la aportación del frasco de aerosol. No se observaron ventajas de limpieza en este sistema en comparación con un accesorio de cepillo. A menudo se utiliza un sistema de cepillos o un accesorio para reducir el uso de disolventes, pero esta ventaja disminuye mucho si se aplica un enjuague adecuado.
Figura 3: Accesorio del cepillo
Figura 4: Placa limpiada con un cepillo (no se utilizó ningún aerosol independiente). No se utilizó ningún enjuague previo ni final. Se muestra un residuo blanco alrededor del QFN B y del QFP, respectivamente.
Figura 5: Placa limpiada con un cepillo (se utilizó un aerosol separado para el enjuague previo y el enjuague final). Se muestran algunos residuos blancos alrededor del QFN B y del QFP, respectivamente.
¿Cuándo es necesario un enjuague final al limpiar una PCB?
En nuestras pruebas, el enjuague final se consideró un paso necesario. Este paso garantiza que todos los residuos de fundente disuelto, que se han eliminado de debajo y alrededor de los componentes, salgan completamente de la placa, y no simplemente cambien de sitio.
A primera vista, lo que recomendamos puede parecer exagerado. ¿Por qué molestarse y gastar tanto en limpiar a fondo debajo de los componentes cuando nadie puede ver la diferencia? Todo se reduce a los requisitos de fiabilidad de los componentes electrónicos. Para los dispositivos electrónicos desechables montados con fundente sin limpiar, un enjuague general puede ser todo lo necesario para obtener resultados aceptables. Si se necesita una mayor fiabilidad, es necesario tener más cuidado, con las técnicas mencionadas anteriormente, para evitar el fallo latente del dispositivo final por contaminación iónica. Dedicar tiempo y esfuerzo por adelantado suele ser una buena inversión.¿Cuál es el limpiador de componentes electrónicos más popular?
Los productos químicos se encuentran en todo el proceso de ensamblaje y reparación de componentes electrónicos, pero ningún disolvente es más común que el alcohol isopropílico. Se utiliza universalmente para la limpieza y como principal constituyente de los fundentes, pero ¿cuánto sabe realmente sobre el alcohol isopropílico?
El alcohol isopropílico (CAS #67-63-0) también se conoce como IPA, isopropanol, 2-propanol, e incluso alcohol para frotar. Disuelve una amplia gama de sustratos polares y no polares, se utiliza a menudo para disolver y eliminar aceites ligeros, huellas dactilares, fundentes de corte, residuos de fundente, depósitos de carbono y la aparición de moho. También es fácilmente miscible en agua, por lo que también se puede utilizar como agente secante.
Para el montaje de placas de circuitos impresos electrónicos (PCB), encontrará alcohol isopropílico, que se utiliza para limpiar los residuos de fundente de las placas de circuitos impresos recientemente soldadas o en la reparación y reelaboración de PCB. El IPA también se utiliza para eliminar la pasta de soldadura o el adhesivo de las plantillas SMT. La limpieza de mantenimiento con alcohol isopropílico es habitual para eliminar el fundente apelmazado y quemado de los hornos de reflujo SMT, los dedos de soldadura de onda, las boquillas de soldadura selectiva, las paletas y cualquier otro lugar en el que el fundente suele acumularse en los procesos de soldadura automatizados.
Hay muchos otros extractores de fundente disponibles para limpiar fundentes concretos, una mezcla más amplia de fundentes y para procesos de limpieza específicos. Póngase en contacto con Chemtronics para obtener más información sobre cómo podemos mejorar su proceso de limpieza de las PCB en el correo electrónico [email protected] o llámenos al 770-424-4888.
Haga una pregunta técnica
Manténgase actualizado sobre noticias, productos, videos y más de Chemtronics.